2. 2. 1 工件预热对涂层质量的影响
在喷焊之前对工件进行预热,主要是使基体与喷焊层的温差减少,降低它们之间由于温差引起的内应力。另外可减缓冷却速度,防止冷却时因收缩发生涂层崩落或产生裂纹。提高预热温度有利于涂层的重熔,能显著地改善涂层的润湿性。但是预热温度过高会造成基体金属的氧化,阻碍涂层与基体的结合,故预热温度不宜过高。预热温度过低,则很容易产生喷焊层脱落、卷边等现象。一定的预热温度既可防止高温粉末颗粒撞击到工件表面时的剧冷、又可以减少喷焊层与基体间的收缩应力差,防止焊层脱落,又不会因预热温度过高而使工件表面氧化严重,破坏工件表面的活化效果。应引起重视的是基材在预热操作过程中,焊枪火焰不能离开预热表面,否则基材表面迅速氧化,影响喷焊质量。预热温度要根据工件的材质、大小、形状和涂层粉末的类型来确定。试验认为,铸铁件预热时采用碳化焰,预热温度控制在200~300 ℃之间喷涂预保护粉为宜。
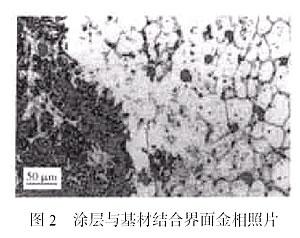
2. 2. 2 预保护喷粉工艺对涂层质量的影响
为了防止零件表面在预热后和喷焊过程中被氧化,在工件达到预热温度之后,应立即在待喷表面先均匀地喷涂一层厚度约为0.1~0.15mm左右的涂层,将喷焊部位保护起来。预保护粉覆盖要完整,喷嘴距离工件表面约80~100mm为宜。试验发现,预保护喷粉时,待熔表面喷覆不完整,在喷焊过程中,出现熔融状态的合金层从边缘卷缩起来,在表面张力的作用下与基材脱离,裸露出的基体表面产生严重的氧化,对此必须将氧化层清除干净才能继续喷焊。预保护喷粉时一般采用还原焰为宜。
2. 2. 3 喷熔温度对涂层质量的影响
在喷完预保护层粉后,对工件继续预热,预热温度达到500 ℃后再进行涂层的喷焊工作。本文采用“一步法”喷焊工艺,喷粉和重熔是同时交替进行的,即边喷涂边重熔。粉末的熔点一般均低于基材,重熔时要靠操作者观察喷涂层表面状态及颜色的变化来控制和调节加热温度,在基材不熔化的状态下保证完成重熔过程。试验中发现,加热温度对熔化涂层在工件表面的润湿效果有明显影响,重熔温度升高,熔化涂层的表面张力降低,使液态涂层容易铺展,提高了涂层的润湿性。当喷涂层在火焰的加热下逐渐变亮,并出现“镜面反光”时,即表明喷涂层已经熔融,此时熔渣上浮,应将火焰立即移到其它部位。重熔温度过高,导致涂层造成流淌,使得喷熔层成形差,出现波浪状、不光滑,影响表面平整程度,润湿性也明显变差,会产生卷边现象。重熔温度过低时,会产生“夹生”现象,熔渣不易浮出表面,喷熔层不能与基材实现良好的微冶金结合,涂层容易脱落,结合强度低。
在喷焊过程中,虽然基体不熔化,但热影响区同样有淬硬倾向,造成基体硬化,易产生裂纹和影响加工性。以铸铁在加热和冷却过程中组织转变行为为依据,采取一定的工艺措施来防止或尽可能减少基体组织的转变。众所周知,铸铁在加热时的组织转变是石墨溶解和碳原子扩散的结果,在温度、固溶度和扩散推动力一定的条件下,原子的扩散距离主要受时间的影响。如果对铸铁的加热速度足够快、加温时间足够短,很显然可以抑制原子的扩散距离,即抑制了铸铁加热过程中的组织转变[2]。随着升温速度的增加,组织转变温度上移。由高温下恒温时间对组织转变体积率的影响,可以看到即随恒温时间的缩短,奥氏体组织体积率明显下降。根据以上理论分析结果,操作时采用越快越好的原则。试验结果表明,将750~900℃的升温时间和喷粉充填时间尽量缩短,控制在4~8s之内,可以改善机械加工性。
本试验是采用中性焰,将喷焊枪的火焰集中在工件表面的一个局部区域进行加热,当该区域的温度达到使工件表面的预保护层粉末开始润湿时,打开送粉开关,将粉末均匀地喷在这个局部区域上,喷到一定厚度时,用同一火焰将这个局部区域的涂层熔融,直到出现“镜面反光”现象后,均匀而缓慢地将喷熔枪移到下一个局部区域,操作中尽可能缩短高温停留时间,对于喷焊量较大的缺陷一次充填不完,可以将火焰移开,待温度降至600℃以下时,再对补焊处重新加热,继续实施补焊,可以防止或减少组织的变化。喷熔时要将工件的温度控制在500℃左右为宜,火焰宜为中性焰或微碳化焰,这样可以防止涂层及基体的氧化而影响喷焊质量。
2. 2. 4 喷熔操作因数对涂层质量的影响
试验发现,喷焊时喷枪移动速度对质量有很大影响。若喷枪移动速度太快,由于热输入小,温度低,粉末来不及熔化或不完全熔化,会产生“夹生”现象,流动性变坏,液态合金的润湿性下降,影响密着性和表面成形,同时涂层中B、Si 的氧化物不宜上浮,产生的夹渣在喷焊层中产生应力源,易使喷焊层崩落,因此必须保证涂层熔化后再移动火焰。若喷焊时运枪速度太慢,喷焊层与基体输入的热输入大,受热时间长,加热温度高造成涂层流淌。因此喷焊时必须控制好喷枪移动速度,试验认为,喷焊速度以80mm/min为宜。
在喷焊操作的不同环节,要求喷枪与工件表面有不同的距离。喷枪与工件表面的距离涉及到涂层的加热温度和直接影响涂层的质量。试验发现,喷熔时喷枪与工件距离过大,加热缓慢,使喷焊层疏松、多孔,喷焊质量差。喷枪与工件距离小,温度高,加热快,熔化迅速,但距离过小,气体对熔融金属吹力大,造成涂层翻泡,成形差且易产生气孔。合适的喷焊距离,保证粉末到达工件表面时具有一定的喷射速度与温度。粉末重熔时喷嘴与工件的距离适当减少,可保证粉末有一定的重熔温度,不会因距离过大而使喷焊层疏松、多孔、质量下降,也不会因距离过小而使喷焊层氧化,以至减弱与基体的结合强度。喷枪与工件表面的距离因喷枪的型号大小不同而有差异,试验认为,采用本试验所用的喷枪,预热时枪距为30~40mm、喷熔时为20~30mm ,重熔时为10~20mm比较合适。也可以采用喷粉的同时进行重熔,粉末不断地喷入熔池,熔池随喷枪的移动而移动,冷却后形成喷焊层。
采用铁基F303粉末喷焊时,因其熔点较高,喷枪与工件距离可适当减小,对加热更为有利。喷嘴与工件距离不可过大,否则喷焊时对熔池的保护作用变差,造成涂层和基体界面产生氧化,影响喷焊质量。喷焊操作时可采用横向用枪、螺旋用枪或喷枪轻微摆动,使涂层加速熔化,这种搅拌作用促进熔渣的上浮,避免涂层的夹渣及火焰对熔融金属的冲击过大而影响喷熔质量。试验发现,喷枪与基体表面夹角75°~85°较为合适。当夹角小于75°时,火焰指向前方,在熔池外生成熔滴,喷焊时粉末易潜藏在熔滴背后,形成所谓遮盖效应,角度越小,遮盖效应越明显,会形成夹生粉现象。当夹角大于90°时火焰指向喷焊层,在气流吹力作用下造成翻毛式大波纹,成形变坏。因此控制喷枪与基体表面夹角,对获得良好喷焊层质量也是非常重要的因素。 |